With the continuous development of science and technology, Inertial Measuring Unit have become an indispensable core technology in modern electronic devices and automation systems. Whether it is driverless cars, smartphones, or spacecraft, IMUs play a vital role. Its powerful motion perception and attitude control functions have shown great application potential in many fields.
What is an inertial measurement unit IMU?
An Inertial Measuring Unit is a device that senses the motion state of an object in real time through built-in sensors. It mainly measures and feedbacks the acceleration, angular velocity and orientation information of an object through sensors such as accelerometers, gyroscopes and magnetometers. The core advantage of IMU is that it can work independently without relying on external signal sources (such as GPS), which enables it to provide accurate position information and attitude feedback in environments with weak signals or no external reference at all.
How IMU works: from perception to calculation
The working principle of IMU is based on the measurement of three main physical quantities: acceleration, angular velocity and magnetic field strength. By processing and fusing these data, IMU can calculate the motion state and direction changes of objects in real time. Specifically, the workflow of IMU includes the following aspects:
Acceleration measurement: The accelerometer in IMU is responsible for measuring the acceleration of the object in three-dimensional space, and the data can be used to calculate the velocity change and displacement of the object. Through accurate acceleration data, IMU can provide accurate relative motion information without relying on external positioning.
Angular velocity measurement: The gyroscope is one of the core components of IMU, which is responsible for measuring the rotational angular velocity of the object. Angular velocity data helps IMU calculate the attitude change of the object and ensure the accurate orientation of the object in space, especially in dynamic environments, where the data of the gyroscope is crucial.
Magnetic field measurement: The magnetometer is used to measure the strength and direction of the geomagnetic field around the object and provide the orientation information of the object. In the absence of external reference objects, the magnetometer helps IMU identify the direction change of the object and ensure the accuracy of its attitude adjustment.
The collaborative work of these sensors enables IMU to not only provide real-time motion monitoring, but also long-term inertial navigation, and is widely used in various fields requiring high-precision positioning.
Main components and classification of IMU
The core function of IMU depends on its internal sensors, which can be divided into different types according to accuracy requirements and application scenarios. Common IMU components include:
Accelerometer: Used to measure the acceleration of an object, usually used to calculate velocity changes and displacement. The accuracy of the accelerometer directly affects the positioning accuracy of the IMU.
Gyroscope: Used to measure the angular velocity of an object to determine the rotation state of the object. The gyroscope is an indispensable component of the IMU, especially for dynamic posture adjustment.
Magnetometer: Measures the strength and direction of the earth’s magnetic field and provides the orientation data of the object relative to the ground. In the case of being unable to rely on other external positioning systems, the magnetometer provides the necessary direction reference for the IMU.
According to different accuracy and application requirements, IMU can be divided into the following types:
Low-precision IMU: Mainly used in consumer electronic devices such as smartphones, tablets, etc. This type of IMU has relatively low accuracy, but is sufficient for simple direction detection and motion monitoring.
High-precision IMU: Commonly used in aerospace, autonomous driving, military and other fields, with extremely high requirements for accuracy. This type of IMU is usually equipped with higher-performance sensors and can provide more accurate data support.
Combined IMU: Combines multiple sensors, such as barometers, thermometers, etc., to provide more comprehensive data support, suitable for applications in extreme environments, such as polar expeditions and underground exploration.
Application of IMU: Wide-ranging impact across industries
With the advancement of technology, the application field of IMU has gradually expanded, and has penetrated into multiple industries such as aerospace, automobiles, robots, and smart devices. The following are typical applications of IMU in several important fields:
Aerospace field
In the aerospace field, IMU is an important part of the aircraft navigation system. In complex flight environments, aircraft often cannot rely on external positioning systems (such as GPS). At this time, IMU can ensure accurate navigation and positioning of the aircraft by monitoring the acceleration, angular velocity and attitude changes of the aircraft in real time. For example, in space navigation, IMU helps spacecraft maintain a stable attitude and ensure the correct heading.
Military and defense
IMU is particularly widely used in the military field, especially in equipment such as missiles, drones, and tactical positioning systems. Accurate IMU data enables missiles to carry out precise strikes, while drones use IMUs for autonomous flight control. In addition, IMU is also widely used in military robots and soldier equipment to improve their combat accuracy and survivability.
Autonomous driving and smart cars
One of the core of autonomous driving technology is accurate positioning and navigation. IMU helps cars achieve accurate driving control even without GPS signals by measuring the acceleration, rotational angular velocity and other data of the vehicle. Especially in complex urban traffic environments, IMU can ensure vehicle stability and reduce safety risks.
Robotics
IMU is widely used in robotics, especially in unmanned ground vehicles (UGVs) and industrial robots. IMU provides robots with accurate motion perception, ensuring that they can autonomously navigate, avoid obstacles and perform tasks in complex environments. Whether it is a service robot or industrial automation equipment, the role of IMU is indispensable.
Consumer electronics
IMU plays a vital role in smartphones, tablets, virtual reality (VR) and augmented reality (AR) devices. They provide a richer user experience by sensing the movement, tilt angle and direction changes of the device. For example, IMU can be used to control the automatic rotation of the mobile phone screen, or track the user’s head movement in VR/AR devices to enhance immersion.
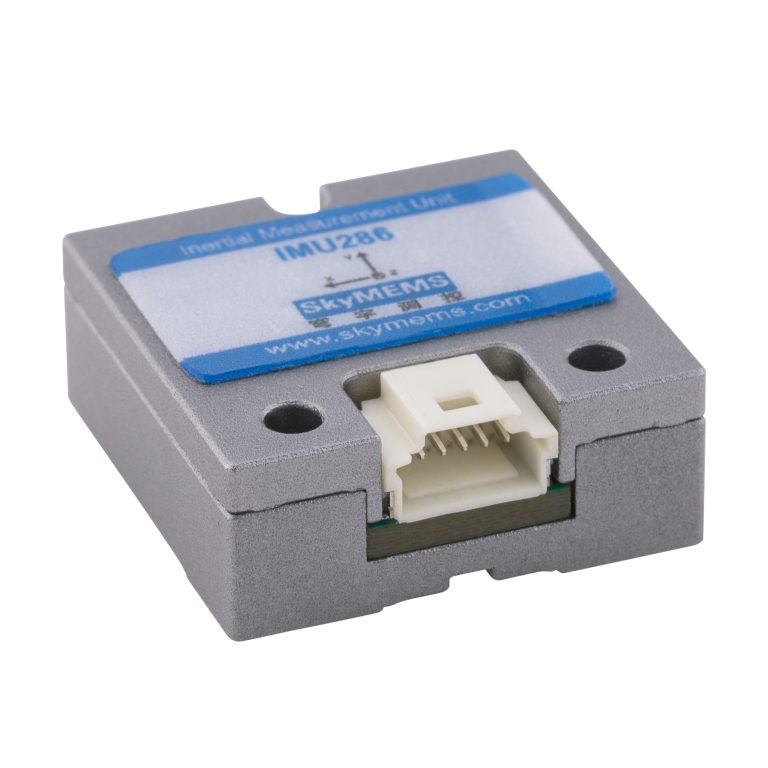
Future Outlook: Potential and Challenges of IMU
With the continuous development of technology, IMU will usher in more innovative applications in the future. IMUs with higher accuracy, smaller size and lower cost will promote the popularization of automation and intelligent technology. From drone flights, intelligent manufacturing to the construction of smart cities, IMU will play an increasingly important role in the realization of comprehensive intelligence. However, IMU technology also faces some challenges, such as the manufacturing cost of high-precision sensors and the impact of environmental factors on accuracy. In the future, with the breakthrough of sensor technology and the continuous optimization of computing algorithms, the application prospects of IMU will be broader.
Inertial Measuring Unit is undoubtedly an important and basic technology in modern science and technology. Its independence and accuracy make it widely used in many fields. From aerospace to autonomous driving, from robots to consumer electronics, the role of IMU is everywhere. With the continuous advancement of technology, the future of IMU is full of infinite possibilities, and it will continue to play a key role in the future intelligent era.