With the continuous advancement of science and technology, various high-precision sensors have gradually entered many fields such as industry, automobiles, and aerospace. Especially in measuring tilt angles and attitude control, MEMS inclinometers have become an indispensable part of modern measurement technology with their high precision, small size, and low power consumption.
What is a MEMS inclinometer?
MEMS (Micro-Electro-Mechanical Systems) sensor is a sensor based on micro-electromechanical technology. It uses the principle of combining micro-mechanical systems and electronic systems to measure physical quantities such as object movement, angle changes, and acceleration. MEMS inclinometer, as the name suggests, uses MEMS technology to measure the inclination angle of an object. It is widely used in scenarios where the attitude and angle of an object need to be accurately detected, such as building structure monitoring, vehicle attitude control, and robot navigation.
Features of MEMS inclinometers:
Small size: MEMS technology has greatly reduced the size of incline sensors, which can be integrated into various devices to adapt to complex working environments.
High precision: MEMS incline sensors have high measurement accuracy and can monitor small angle changes in real time to ensure data reliability.
Low power consumption: Compared with traditional motor or liquid tilt sensors, MEMS tilt sensors have low power consumption and are very suitable for long-term monitoring.
High reliability: Due to its simple structure and the absence of complex mechanical parts, MEMS tilt sensors can work stably in extreme environments and have strong anti-seismic and anti-interference capabilities.
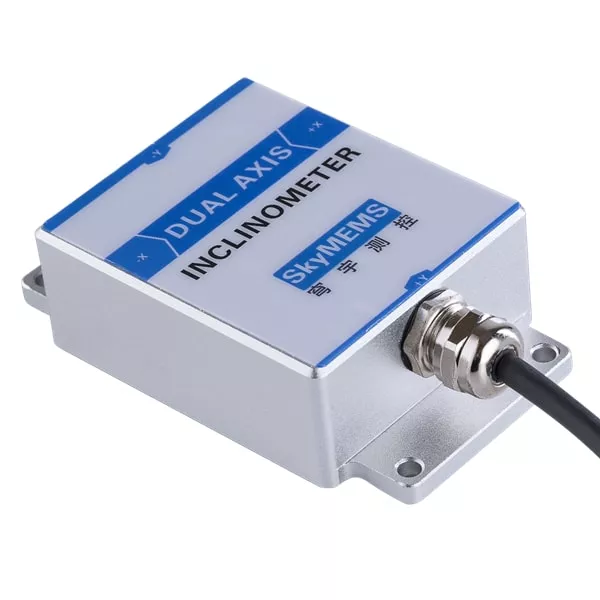
Working principle of MEMS tilt sensor
The core working principle of MEMS tilt sensor is based on acceleration detection of micro sensors. Inside the MEMS tilt sensor, there is usually a micro mass block, which is suspended in a set of micro spring systems. When the sensor is affected by external gravity, the mass block will displace, and the circuit inside the sensor will measure the tilt angle in the direction of gravity according to the displacement change. This principle can provide high-precision tilt data through real-time measurement of angle changes.
In addition, MEMS tilt sensors realize sensing and signal conversion through capacitors, resistors or piezoelectric elements. Its output signal is usually an analog signal or a digital signal, which is convenient for integration and processing with other devices.
Application fields of MEMS tilt sensors
The high precision and high reliability of MEMS tilt sensors make them widely used in many fields. Below we will focus on several typical application scenarios.
1. Building structure monitoring
In the construction industry, MEMS tilt sensors can be used to monitor the inclination of buildings in real time and help assess the safety of buildings. Especially for structures such as high-rise buildings, bridges, and large towers, monitoring their tiny inclination changes can effectively avoid safety hazards caused by factors such as earthquakes, wind or foundation settlement. Through the real-time data of MEMS tilt sensors, engineers can take timely measures to ensure the stability and safety of building structures.
2. Automation and robot navigation
With the development of automation technology and robotics technology, MEMS tilt sensors have become one of the key components in robot navigation systems. During the robot’s walking, handling, and operation, MEMS tilt sensors can accurately measure the relative angle between the robot and the ground, helping the robot to achieve accurate positioning and path planning. In addition, MEMS tilt sensors are also widely used in attitude control and dynamic stability adjustment in automated control systems.
3. Vehicle attitude control
MEMS tilt sensors are also widely used in intelligent vehicles, driverless cars, off-road vehicles, and other fields. In these vehicles, MEMS tilt sensors can detect the vehicle’s inclination angle and attitude changes in real time. Especially in scenarios such as off-road driving, ramp start, and rollover warning, MEMS tilt sensors can provide high-precision data support to help the system adjust the vehicle’s motion trajectory and stability in real time.
4. Agricultural equipment
In the field of agricultural machinery, MEMS tilt sensors can be used for posture monitoring of agricultural equipment and crop growth environment control. For example, automated sprinkler equipment, unmanned agricultural machinery, etc., monitor the tilt angle of the equipment through MEMS tilt sensors, thereby achieving precise operation control and improving operation efficiency and safety.
5. Aerospace
In the field of aerospace, MEMS tilt sensors are widely used in navigation, attitude control and other systems. Especially in equipment such as drones, satellites, and rockets, MEMS tilt sensors can provide high-precision real-time data to help equipment maintain a stable flight state and accurate navigation path.
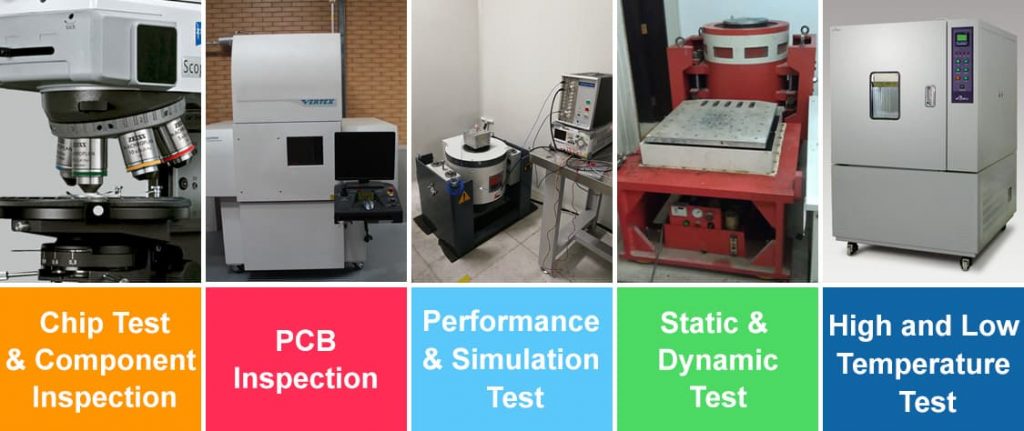
Advantages and challenges of MEMS tilt sensors
Advantages:
High precision and high stability: MEMS tilt sensors have very high measurement accuracy and can provide real-time data of small angle changes, which is crucial for fields that require precise control.
Miniaturization and integration: Because MEMS technology greatly reduces its size, MEMS tilt sensors can be easily integrated into various devices to adapt to complex working environments.
Low power consumption and high reliability: Compared with traditional mechanical tilt sensors, MEMS tilt sensors have the advantages of low power consumption and long operation time, and are especially suitable for remote monitoring and unmanned equipment.
Strong anti-seismic and anti-interference ability: MEMS tilt sensors have no complex mechanical parts, so they have stronger anti-seismic and anti-interference capabilities, and can operate stably and for a long time in harsh environments.
Challenges:
Impact of temperature changes: Although MEMS tilt sensors perform well in most cases, the performance of the sensor may be affected to a certain extent under extreme temperature changes. Therefore, it is necessary to pay attention to its operating temperature range when selecting.
Long-term stability: Although MEMS tilt sensors are very durable, after long-term use, the zero bias error of the sensor may gradually increase and require regular calibration.
V. Future development trends
With the advancement of science and technology, MEMS tilt sensors will become more intelligent and precise in the future. With the continuous improvement of material technology, micromachining technology and integrated circuit technology, MEMS tilt sensors will play an important role in more high-precision measurement fields. For example, with the rise of industries such as smart manufacturing and unmanned driving, MEMS tilt sensors will further promote the development of automation and intelligent equipment.
In addition, future MEMS tilt sensors will pay more attention to multifunctional integration and be able to work with other sensors (such as accelerometers, temperature sensors, etc.) to provide more comprehensive data support and meet the needs of different application scenarios.
MEMS tilt sensors, as a high-precision, low-power measurement tool, have been widely used in many industries, and with the continuous advancement of technology, their application prospects will be broader. Whether in building structure monitoring, automation equipment, aerospace, or in the fields of intelligent transportation and agricultural machinery, MEMS tilt sensors will play an irreplaceable role. Through continuous innovation and research and development, MEMS tilt sensors will surely bring more value in a wider range of fields and become an indispensable core component in the era of intelligence.